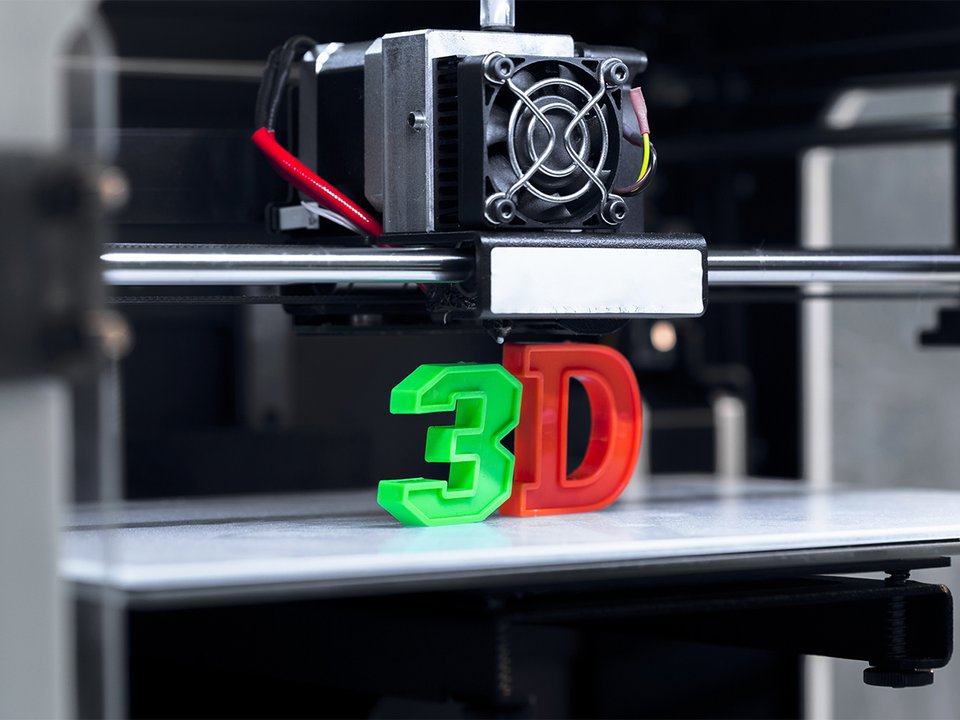
The only constant in life is change; additive manufacturing (AM) is expected to revolutionise the way products are designed, manufactured and distributed.
Could ordering a replacement part for your ship be good for the environment as well as your wallet? The answer may soon be a resounding “yes” thanks to the power of AM, also popularly known as 3D printing.
In the not-too-distant future, ships managed by Bernhard Schulte Shipmanagement (BSM) will be able to order parts via a digital warehouse that contains the electronic information needed for 3D printing. This information will be shared with a contracted AM provider who can proceed to manufacture the part and fulfill the order.
Digital Innovation in Shipping
With a growing network of AM providers, it will be possible to print parts at the vessel’s next port of call and deliver it within the quickest possible time. This represents a significant improvement over the current model of spare part procurement and supply for ships that requires supply chain and transport costs, coordination between several parties, and compliance with state regulations.
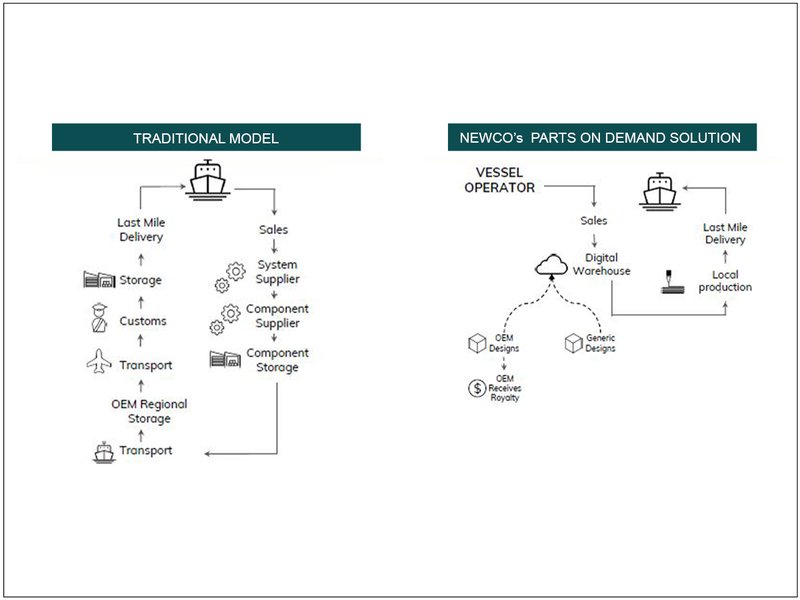
Traditional model versus AM supply of ship spare parts.
“At BSM, we believe the technology has the potential to help with reduction of greenhouse emissions while lowering the carbon footprint from air and other transport,” said Hardy Romahn, BSM’s Singapore-based Group Technical Manager for projects. “In addition to producing orders close to the place of need, additive manufacturing will enable us to improve the availability of obsolete parts or parts with a long lead time”.
AM utilises computer-aided-design (CAD) software and 3D object scanners. The 3D printer application directs the hardware to lay down the required material in one layer after another in precise geometric shapes, eventually creating useable objects such as ship parts. Additive manufacturing works best for a wide variety of goods in small quantities, enabling it to serve the market for made-to-order items, from customised medical devices to hard-to-find machinery parts.
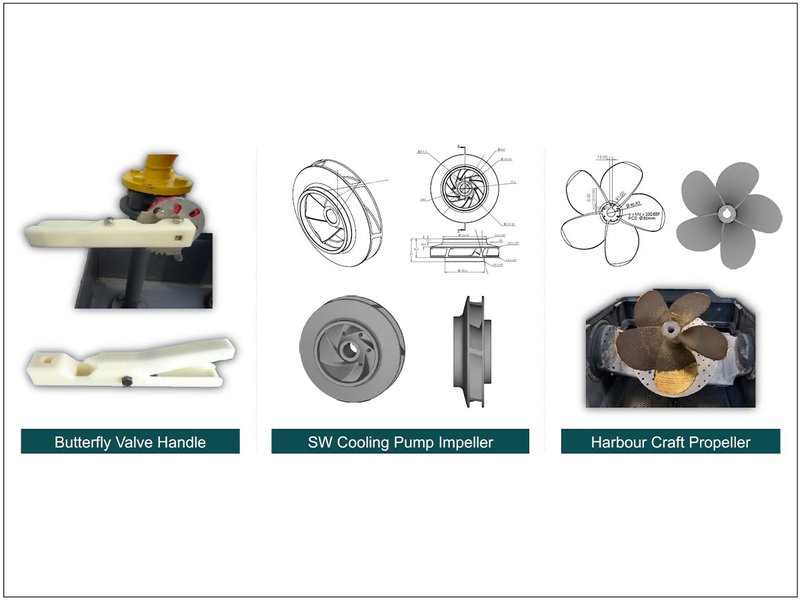
Examples of 3D printed ship parts.
Outdated but not Obsolete
The average lifespan of a ship is 25-30 years. That’s a long time in our fast-paced modern world where smartphones are obsolete in ten years due to a lack of replacement parts and software support. 3D printing can prevent older ships from becoming fossils by making obsolete replacement parts for it.
Once the technology is further implemented, BSM will be able to react faster to part requirements. At the same time, it will be possible to modify and improve parts with different materials to make them lighter or stronger, according to Romahn.
In October 2020, Wilhelmsen’s Marine Products division and Thyssenkrupp signed a joint venture letter of intent to re-examine and optimize the production and delivery process of 3D printed spare parts for the maritime market. The Schulte Group joined this industry program in early 2021 to examine the potential of AM by jointly carrying out feasibility and pilot study projects on the printed products.
“It’s not an easy process because you need drawings and photos from the ships and there are still a lot of questions that need to be answered,” Romahn said. “As part of this research process, it’ll allow us to find out which parts are possible for 3D printing, and which aren’t so suitable.”
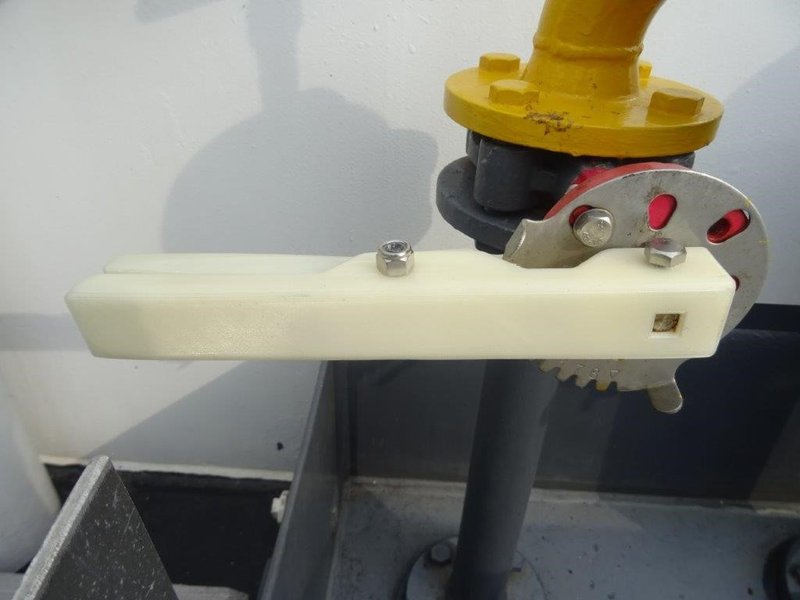
3D printed butterfly valve handle fitted, in use on vessel.
“The important thing is to build a repository of knowledge and expertise based on vessel needs and clients’ demands,” added Romahn. To date, his team has received two requests from ships directly to trial the printing of a pump impeller and valve handle while the working group is trialing the printing, certification and approval of a cooling water pipe connector for a BSM-managed vessel, the “Rosco Poplar”.