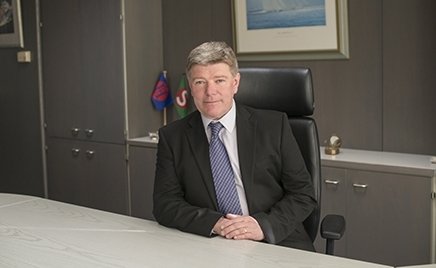
David Furnival, BSM’s Chief Operating Officer (COO), does not hesitate when asked the question: “What is the most important issue for Bernhard Schulte Shipmanagement today?” Based on the Isle of Man and recently appointed as President of The Society of International Gas Tanker and Terminal Operators (SIGTTO), David replies: “Operating efficiency is the key area of focus given the difficult state of most shipping markets with many of our customers under pressure as result.”
“When customers entrust their vessels to BSM, it is absolutely vital that we are able to demonstrate the highest levels of operating efficiency combined with an uncompromising approach to safety and quality. That is the main reason why they use our services,” he says.
BSM measures operating efficiency in two main ways. One is examining operating expenditure (OPEX) on each managed vessel; the other is through monitoring the reliability aspects of vessel machinery in a holistic, analytical way.
With respect to operating expenditure, BSM has participated in a study by the Boston Consulting Group (BCG) over the past three years that benchmarks OPEX performance against owners who are managing their vessels directly. “We have been 10%-11% below the average OPEX of owners included in the study sample over the past three years. The issue now is that owners’ OPEX is falling faster each year, as they react to ongoing difficult markets, so we must continue to find ways to stay ahead to maintain our advantage.”
Fuel efficiency and its monitoring is one way of maintaining this advantage. David says that crew training, retention of knowledgeable seafarers and personnel, as well as reporting discipline are all vital aspects in keeping ahead of the game in fuel efficiency. The company will soon gain ISO 50001:2011 Energy Management Systems accreditation and will be among the first ship managers in the world to obtain this global standard.
The maintenance of machinery is also closely allied to maintaining high standards of operating efficiency. “We have worked hard on this in the past few years and today our maintenance and repair teams can tackle any kind of issue anywhere in the world, from an overhaul of main or auxiliary engines to supervision of a standard dry-docking or a major overhaul including crew training.”
Developing this theme, David explains that a major step forward will come when BSM implements its ‘Fleet Performance Monitoring Platform’, encompassing new software which enables a fully integrated approach to planned maintenance. “The platform will allow us to adopt a condition-based and, ultimately, predictive maintenance approach and we will be capable of conducting a detailed analysis of all technical aspects of a vessel,” he explains.
“We look at ‘underlying factors’ of mechanical performance on board and we take pre-emptive action.” An example is the use of vibration analysis of ball and roller bearings used in machinery. “We analyse changes in vibration data to determine the condition of a bearing and this allows a safe extension of time between overhaul and timely intervention before a failure occurs.”
Of course, this kind of performance analysis needs to be aligned with an effective loss prevention, safety and quality culture. David, as a former seafarer himself, understands the focus that must be placed on crew safety. “Like all ship managers, we face significant challenges in this area. The personal safety of our seafarers, and all third-party personnel on board our vessels, is fundamental. In the past six years the number of injuries on board our managed vessels has halved. However, we can never be complacent with respect to personal safety and we are always seeking ways in which to create safer working environments.”
Striving to continuously improve in all aspects of its operations, BSM places great emphasis on the identification and development of innovative ideas and practices. Two examples of projects that are being progressed are the ‘Innov8’ initiative and ‘Project Pilot’. ‘Innov8’ is a programme in which all BSM employees, both sea and shore based, are encouraged to come forward with innovative ideas to help improve the way things are done; it has become valuable in driving the development of new ideas across the company.
“BSM believes that great companies have people who can come up with a hundred good, small ideas to make things better. It’s rare for anyone to conceive one big idea and our experience shows that many small ideas add up to real improvements!”
Aiming to promote the initiative, BSM rewards employees who propose an idea that the company then adopts. Seafarers also have access to an online portal through which they can suggest ideas. “It works really well and each year we get around 30 good ‘Innov8’ ideas. This is a very satisfying part of my role when I see these actually implemented,” David adds.
‘Project Pilot’ began two years ago and was developed from studying techniques used by the aviation industry. BSM has now produced concise, easy-to-understand operational procedures in clear, simple English. The first procedures to be revised in this form were those covering navigation and ship handling in the Marine Manual, followed by other priority manuals such as emergency response. Most manuals, both shipboard and office, are now rewritten in Project Pilot format and the remainders will be completed within 2017.
David says ‘Project Pilot’ was a much-needed initiative aimed at making procedural understanding and communication easier at all levels, as well as promoting better teamwork. “Processes are now unified, with better cross-checking and the feedback we have received from our crew in particular, as well as the shipping industry in general, has been encouraging,” he emphasises.
Supply chain management is another area that David and his team are focused on to further improve operating cost efficiency, with progress made in centralized procurement and reducing the number of suppliers. “While fewer suppliers means better negotiating positions for BSM, it also encourages long term supply chain partners to work hard to produce better outcomes for both sides.”
With little sign that shipping’s difficult times will disappear soon, David says that BSM must be relentless in its efforts this year to achieve even greater operating efficiency. “I will keep saying it: the reason why our customers entrust us with management of their ships is because we deliver maximum vessel availability, safety, reliability and cost efficiency. So, in these testing times, we must deliver on this promise,” he concludes.